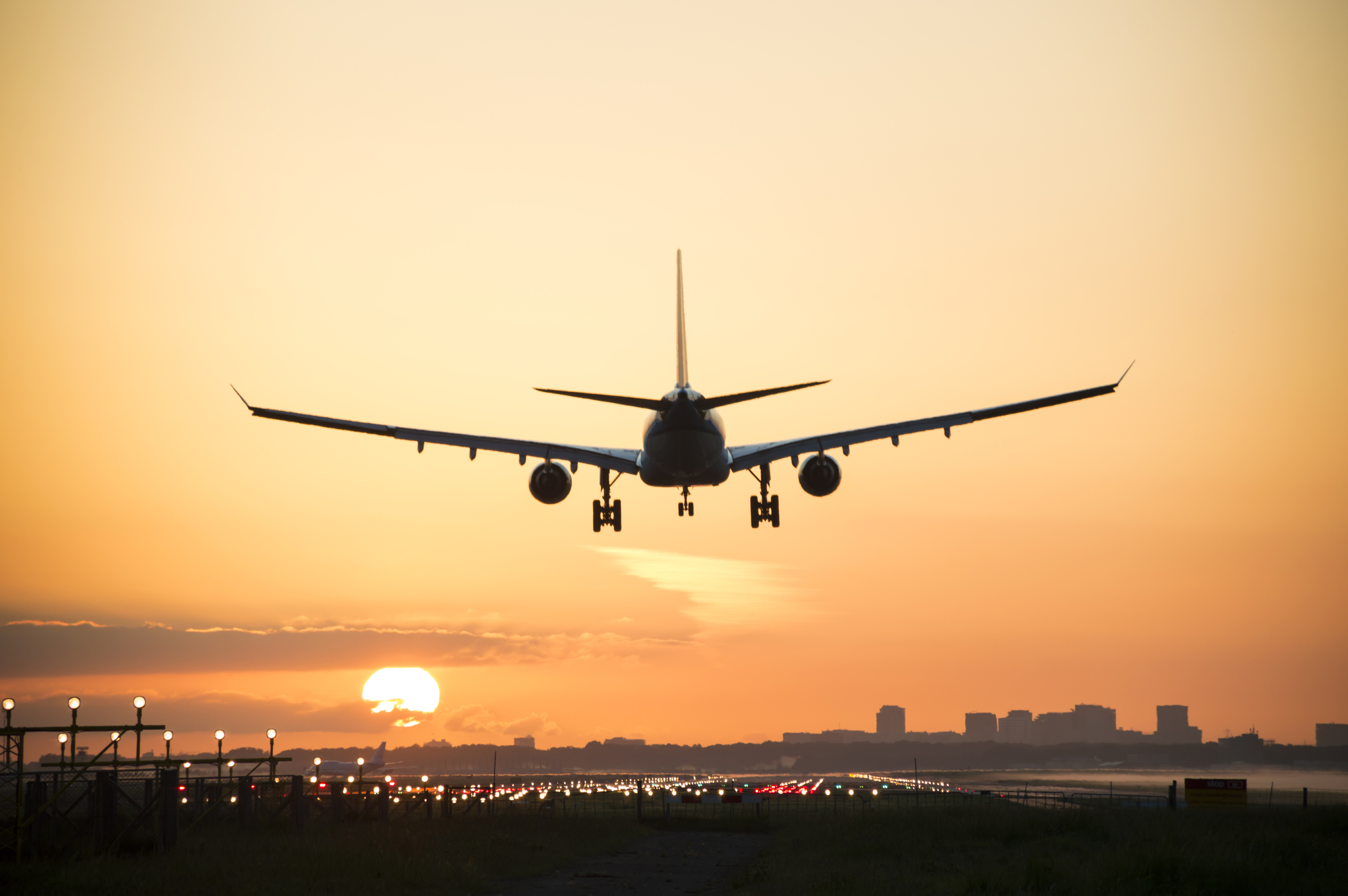
Conversation of a detached production site into an autonomous plant
Our client acquired a detached production site of a T2 automotive supplier and started a similar production program for the aviation industry. The possible transfer of know-how from the mother company was limited and there was a number of technical, organisational and supply-chain related challenges to be solved with clients and suppliers in a a plant with a non-functional middle-management. Agim were asked to provide an IM with the following tasks:
- to optimise production planning and ensure delivery of products in time
- to ensure the proper usage of the existing ERP system for manufacturing and logistics
- to hire qualified and motivated staff
- to find and contract partners for cooperations within peak-periods
The success: The AGIM IM fine-tuned the capacity planning in order to enable weekly forecast and found external sources for peaks. He optimised order planning working directly with the mother company and the clients. He ensured training for the ERP system and got staff to use it on a daily basis. He run an inventory achieving 100% of accuracy of the data in the system compared to reality. He prepared a plan for possible cost reduction and the further development of the ERP system and handed all activities and plans over to the newly hired Plant manager.